The Surprising Advantages of Augmented Reality Support.
- SGA
- May 24, 2021
- 2 min read
Have you ever been in the situation where you need your control systems fixed asap, but are finding it difficult to explain your problems over the phone or email? Video calls have been a solution to this problem for a little while now, but fortunately, there's a new technology that can offer more advantages when providing remote support.
Video calls can be extremely useful when it comes to providing remote assistance for any support problem that needs to step ‘beyond the console’.
Simple examples would be:
Cycling power to the hardware.
Plugging in diagnostic cables.
Disaster recovery changeovers and equipment swap out.
However, the problem with video calls is that even though the medium is so visual, it can still be subject to miscommunication. For example, if you're receiving assistance from a support provider and they say this to you, “See the red switch, flick that one... No, not that red switch, the other one”. It can quickly become quite confusing and time-consuming in solving the issues. Misinterpretations or poor descriptions can lead to poor outcomes and in the best-case scenario, these communication errors are time costly but in the worst case, it could be much more disastrous.
Augmented Reality (AR) has become a rising trend in technology and individuals are beginning to find innovative solutions for AR, including remote support. Similar to a video call, AR remote support allows you to simply show your support provider the issues in real-time by using an AR app and the video function on your smartphone.
However, the difference between AR and video support is that AR provides the ability for parties of the video call to place or draw “virtual markings” on objects in the video call. Through the power of AR, those markings stay ‘locked’ with the marked objects as the video screen is moved around.
For example, let's say the on-site technician points his camera at the PLC. The remote engineer can place an accurate marking on the position of the port that he needs the technician to plug the cable into. Even if the technician subsequently moves his camera view, the marking previously placed stays locked on to the location of the port. Allowing the Technician to easily work with the equipment, without losing the placement of the selected port.
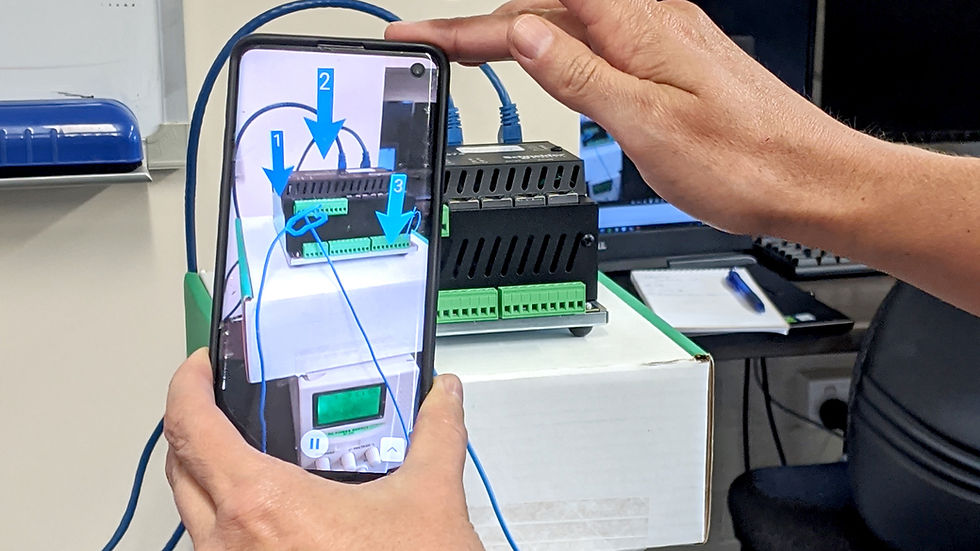
Similar technology can also be used to develop clever operations manuals for engineers that ‘know’ the equipment and can guide technicians around their equipment, highlighting relevant components and providing visual and contextual information on their smartphone.
At SAFEgroup Automation (SGA), we have researched a few different market solutions in this area and reviewed the following two solutions:
These solutions aren’t the only ones in the market and we’d be happy to provide services to assist you with a wider market assessment if required. While the technology isn’t perfect, we were actually pleasantly surprised at its ease of use and its benefits to various applications and would recommend that our clients consider it.
As a side note, if you're looking into AR and have kids at home, make sure you try out Googles 3D augmented reality animals.
Comments